With the standardization of working environment and machine operation, the quality control of pre-press production plays a pivotal role in rotary printing cylinder. If the pre-press work is not in place, the pre-press production is not suitable for commercial rotary printing, then it will cause a delay in the rate of genuine products, a lot of waste of paper, and will seriously affect the quality and timeliness of their products. To give full play to the advantages of commercial rotary printing, pre-press production to meet the actual needs is indispensable.
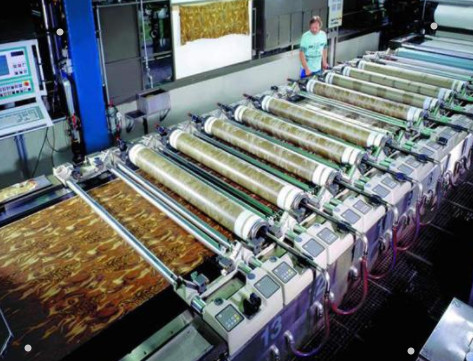
I. Pre-press production process of
rotary printing cylinder1. Design: High-speed commercial rotary printing cylinders generally use web printing, the paper path is relatively long, the physical and optical properties of the paper surface is not very uniform, mainly by drying to accelerate ink drying, pre-press design has different requirements from lithographic offset printing and newsprint offset printing.
(1) the use of gray component replacement: GCR (GreyComponentReplacement abbreviation) means that in the color image reproduction, where the three primary colors of ink overlay or mixed into the complex color area of the non-color value, can be used with the three primary colors of the weakest ink color equal to the ink color to replace, and get the same visual effect.
In the production of the actual process, sometimes some big box stores of the commodity flash (referred to as DM single) ink color is difficult to adjust, especially the large area of dark or field part, the reason, in fact, is Y, M, C version is too heavy, it is difficult to achieve a neutral gray balance, found after many times through practice, yellow, product, green each color version are deep, not only the ink color is difficult to print evenly, easy to paste version and is not conducive to the standard. In the front-end production must use GCR technology to increase the depth of the black version, black to replace the neutral gray, reduce the amount of ink used in other colors, so that when printing, as long as the black version is normal, the other color version even if the amount of ink has slight fluctuations, the color of the print is easy to maintain stable, these are mainly due to the role of the black version of the skeleton. By reducing the amount of color ink, not only easy to achieve the sample requirements, and reduce production costs.
(2) the use of undercolor removal Undercolor Removal (UnderColourRemoval, abbreviated as UCR) and the above-mentioned GCR is different, GCR that is, non-color structure process, is the full order of the undercolor removal, while the undercolor removal is part of the removal, the black version is a short version.
rotary printing cylinder printing, often appear sticky dirty, pile of ink, the title or the field is false, these phenomena on the one hand can not exclude the use of paper, ink printing suitability and equipment factors, but part of the reason or pre-press design is not well combined with the actual requirements of printing production.
Pre-press design causes sticky dirty cause is the total value of the picture order, that is, the total amount of ink set unrealistic, without drying the total value of the cold-set ink order and the provisions of the single sheet of paper does not exceed 260%, while the heat-set web printing does not exceed 300%. Many people do not understand these, only the pursuit of color fullness, the total value of the order and set very high, resulting in the field pressed out of the title or a large area of the darker part of the pile of ink, faint, thickening of the ink layer at the same time also requires drying temperature rise, resulting in increased surface wrinkles of the print. And in the case of high order value of the total will occur, such as overprinting is not firm, the back of the print and the back of the ink is not sufficiently dry to produce dirty and other phenomena
In the process of continuous printing practice, to find effective solutions: 1.
1. Reasonable setting of the total value of the picture tone, and as far as possible below the national standard value, so that the printed image can be both level and clarity, while reducing the ink drying time, so that the print is not easy to stick dirty.
2. Reasonable use of base color removal.
Part of the removal of the base color, reasonable control of the neutral gray balance, widen the image contrast, increase saturation. This can effectively ensure that the picture color is vivid, and not easy to stack ink, dull. Considering the commercial rotary printing dot expansion, with about 90% of the deep network instead of the field, to solve the title or the field of faint, off-color is very effective.
3. Printing plate drying
rotary printing cylinder adopts the design of the blanket cylinder for each other as the embossing cylinder of soft pressure soft, the paper in the blanket cylinder under the roller to complete the ink transfer, dot expansion (mainly mechanical dot expansion) is much larger than the sheet-fed offset press, detected in the process of multiple printing, for different papers, while taking into account the mechanical and optical dot expansion, with X-Rite528 spectrodensitometer to measure the Heidelberg M-600 printing on the normal, printed dot expansion in general 13% to 19%. In the production of commercial rotary printing plates used to increase exposure to 3% and below the exposure of small dots.
Mechanical dot increase by many factors, such as: ink, fountain solution, blanket, paper surface properties. Optical dot increase is mainly due to refraction of light to increase the apparent area of the dot. Because the dot area expansion will have a certain impact on the grayscale of the print and the balance of each color, degree 13 ladder scale section sun off the third level, Yin and Yang micron concentric circle coil section 8μm Yin and Yang line corresponds to the Qi. If not 175 lines / inch, according to the actual situation of each printing plant to make reasonable adjustments.
4. Printing plate scanning
rotary printing cylinder printing speed is fast, before reaching the normal ink color and registration, there will be a large number of scrap and substandard products. In order to improve efficiency, the early emergence of qualified prints, reduce unnecessary waste of ink, paper, etc., pre-press production should be used to scan the printing plate. It can control the color difference between the print and the designer to a small extent.
General plate scanning can reach the actual printing when the normal amount of ink required for the print about 80%, and then through the adjustment of the overall ink characteristics curve, you can quickly produce the right product, can greatly improve efficiency, especially important for those without proofing printing work, plate scanning work on those with proofing of short-run printing is more obvious, it can greatly reduce the commercial rotary machine to open the normal Ink color time, saving down a lot of paper, ink and other raw and auxiliary materials, reducing costs and increasing benefits for enterprises. If you encounter the scan out of the curve and the actual printing when the normal ink curve difference between the prints, in the pre-press generally check the following aspects.
First look at the edge of the film trailing edge of the long iris width is correct, the width of different models of red film is different, for example, the Heidelberg M-600 perimeter of 598mm roller requirements for the red film width of 23mm, while the M-600 perimeter of 578mm roller requirements for 23.1mm, and the greater the difference between the actual required width, the greater the scanning results are affected, therefore, the actual operation to Therefore, the actual operation should be combined with the model used, and the field block of suitable width should be tanned by red film.
Second, check whether the smoothness of the plate used is ideal, sometimes the plate has a depression, the surface is not flat, the scanning results will also be affected. Generally the flatness of the domestic printing plate is slightly inferior compared with the original imported foreign plates. Of course the impact caused by unevenness of the plate can be attenuated by adjusting the intake of the plate scanner. Generally, when scanning imported plates, choose the suction volume level one, while scanning domestic plates can choose two or three suction volume, depending on the plate surface flatness flexible use, because after increasing the suction volume, will make the plate more flat adsorption in the scanning panel, which is conducive to the correct reflection of the plate on the graphic part of the ink demand situation. However, blindly increase the amount of suction may be sucked into a large amount of dust, a long time will be blocked suction holes, affecting the quality of scanning.
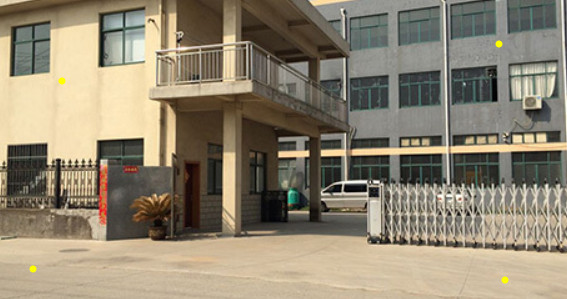
In short, in the pre-press production should gradually realize: only pre-press production to adapt to rotary printing cylinder, not to adapt to the
rotary printing cylinder to pre-press production. rotary printing cylinder pre-press production is complex and profound, need to be in the actual work of In order to continuously improve the production level, it is necessary to continuously explore and summarize in the actual work.
View More(Total0)Comment Lists